Many of us have heard or experienced the Fear of Missing Out (#FOMO), especially in a world of Facebook and Instagram. APR can’t help there, but we can definitely help with the Fear of Running Out (#FORO).
And what if FORO is affecting your ability to give others FOMO? This is when you are on vacation, but worried that the person covering for you may forget to order something that can cause a press to shut down.
FORO is also known to cause #FOEF, Fear of Extra Freight, which occurs when items need to be sent over-night or multiple orders are placed when one order would have reduced freight and handling costs, or #FOTMOI, the Fear of Too Much or Obsolete Inventory, or.…well you get the picture.
How can SupplySentry help?
SupplySentry is an RFID-Based Inventory Management System and Customer Portal that results in eliminating stock-outs by providing real-time information which lets you focus more on your business and less on worrying about outages for critical products needed to keep the presses running.
Managing inventory levels of such products as stickybacks, tapes, doctor blades, and other miscellaneous items can be labor-intensive and time-consuming but running out of any of these items can cause a press to shut down or create unwanted schedule changes. Even careful attention to stock levels can be suspect if requirements change quickly due to unforeseen events. Typical vendor-managed inventory or consignment programs can fall short as they are dependent on periodic counts vs. real-time information.
SupplySentry provides a reliable real-time inventory management system integrated with a user-friendly interface that reduces "#FORO", optimizes inventory levels, and saves time. We also combined this with a fully searchable information portal that includes product data, SDS sheets, and product usage tips.
Usually when asking customers if they ever run out of stock with their consignment or their current process the answer is “yes, often” creating several issues including added overnight freight costs or press schedule changes. And, we see a lot of customers who receive too many shipments per month to avoid #FORO. This results in higher annual freight expenses.

By having a more real-time solution with the ability to rapidly determine any changes in usage patterns and set up replenishment rules based more on just-in-time criteria, a printer can both reduce #FORO and reduce total costs.
APR’s SupplySentry is based on years of software development where we have consulted with inventory management experts to create predictive analytics that optimize the amount to have in stock and when and how much to replenish. Installations are customized to be configured as a special cabinet, racking system, or a complete room based on need and physical location. All items that are to be tracked by the SupplySentry system are supported by APR’s five warehouse locations.
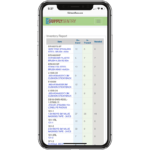
SupplySentry's web-based interface allows the customer to see what items they stock, the quantity of each item on hand, the quantity in transit, and the suggested amount needed to replenish their supply. The user interface also gives customers various information and reports showing what their usage is by product, by period. And, our new mobile App makes the availability of what you have in stock or on order even easier to access in today’s busy environment.
SupplySentry currently has over 50 installations at many major converters throughout the country. The systems manage hundreds of SKUs and millions of dollars worth of inventory all on a real-time basis.
What SupplySentry customers are saying:
“We utilize RFID SupplySentry technology on a daily basis. Without it, time spent on supply inventory and ordering would create unnecessary delays in several facets of production.”
“The peace of mind that whenever we use up an item, the RFID cabinet will always have what we need. We don’t have to call, wait for a shipment, or keep track of our supply inventory.”
“Controlling everyday production supplies without having to manually count & order is just more efficient for everyone in production.”
“Having RFID SupplySentry technology take care of that portion of our supply needs, frees me up to work on other areas of my job. It’s definitely one big item off my plate.”
“Our Supply Sentry RFID Cabinets have made our job so much easier. We no longer have to take an inventory and send out an order, but instead, the RFID cabinet handles all of our orders and inventory. This saves us time to look for improvements elsewhere and has helped eliminate any mistakes when it comes to reorders. Double thumbs up!!”
“We have been using SupplySentry for years now. This system works so well that we have installed it in different areas of our facility. APR makes it easy to control our inventories, so we don’t run out of items that are necessary for our plants to run.”
“I know the inventory will be ordered on time. We have never come close to running out of product. We don’t have to rely on someone to order the product. We always get an order notification from APR when the order is ready to ship.”
“Supply Sentry RFID has reduced our concerns and time spent on tracking inventory for our plates and mounting tape. This allows our people to focus on the quality of our finished product.”
“APR’s Supply Sentry RFID system has been an asset to our company. It has worked flawlessly allowing excellent inventory management of our product.”
“Just like to say thanks for introducing us to the RFID system. This system has taken away all of my time and worries about inventory and ordering of our mounting tapes.”
“I have been working with inventory management for 10+ years and have used inventory lists, Kanban systems and the Supply Sentry RFID program from All Printing Resources has made inventory management easy and friendly to use! It’s a simple, one stop shop and alleviates many inventory related headaches!”