RFID-Enabled Supply Management System Provides Real-Time Inventory Information
Established in 1902, American Packaging Corporation (APC) is a family-owned flexible packaging converter and renowned leader in the North American packaging industry. With over a century of experience serving a wide range of markets, APC specializes in flexographic and rotogravure printing, multi-ply extrusion, and adhesive lamination of film, paper, and foil, as well as pouch and bag fabrication to meet a variety of requirements.
Over its long history, APC had surprisingly experienced only one major ownership change when the Schottland family purchased the company from the Kardon family in 1986. Today, APC operates five Centers of Excellence in the United States (located in WI, IA, and NY) and employs approximately 1,000 talented, motivated professionals, including nationwide sales reps and field technical support.
APC has built a reputation as the go-to source for effective solutions in flexible and specialty packaging, serving the unique needs of a multitude of end-use segments and the most demanding applications. They are able to uphold this reputation by “delivering more unmatched quality of materials, unparalleled customer service and the most innovation possible, delivering a high-quality product on time, every time.”
The Challenge
In 2010, APC began searching for a more efficient way to keep count of its supplies inventory. They often found themselves running out of material, requiring expedited shipments and internal resources dedicated to managing inventory across their facilities and departments. One example is how they were tracking their tape usage. With over 45 different tapes used regularly, it was challenging for the company to ensure that the correct tape quantities were on hand to meet changing business demands and consumption requirements.
One of APC’s core values is innovation, and they were open to pioneering new approaches in their search to implement more efficient continuous improvement practices. The company evaluated several inventory management solutions during the initial project. They analyzed current internal time studies and then reviewed each system based on the cost of implementation, post-implementation labor allocation, reliability, and added supplies costs.
Ultimately, they turned to All Printing Resources (APR) for recommendations on overcoming their inventory challenges. APR and APC have had a long-term supplier relationship, and according to Robert Jamison, Printing Manager, “APR has been our valued partner for supplies management, Esko equipment, and training for several years. We were confident they could provide us with an innovative path forward.”
The Solution
APR recommended SupplySentry -- a management system that can be used for almost any plateroom or pressroom consumables (including photopolymer plate material, stickybacks, tapes, doctor blades end seals, safety supplies, cleaning supplies, and more.)
With SupplySentry, supplies are placed in an RFID-enabled area (e.g., shelf, cabinet, or full inventory-managed room). All products are shipped from APR with an RFID tag, and the system keeps track and automatically reorders supplies. SupplySentry customers have access to real-time information on their inventory levels and know what they have in stock at any given time. The system automatically re-stocks the supplies, eliminating the need for an appointed employee to spend time doing so, in addition to eliminating unnecessary repeat orders and outdated inventory sitting on shelves. Today APR has over 60 SupplySentry customers in the market.
The Outcome
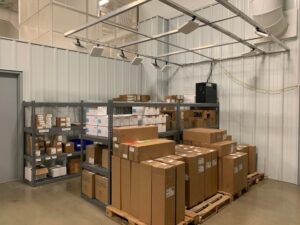
Supply Sentry was first installed on four cabinets at APC’s Story City, IA location in 2011. As the facility grew, an additional RFID shelf was added in a secondary location inside the facility in 2015. In 2020, a supply room was constructed to allow for further expansion of the system and encompass increased volumes of inventoried items.
The company added the inventory capability in DeForest, WI. When they built a new greenfield flexographic printing and laminating facility in New York in 2018, they scoped in a full inventory room. They will also be adding SupplySentry to their Columbus, WI facility this year.
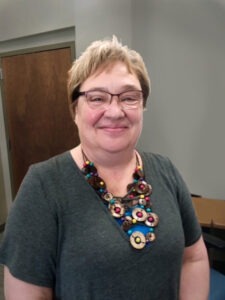
Maintenance Clerk
Each of these installations has gone quickly and smoothly, and APC’s employees have been very receptive to the system as it has eliminated the need for daily or weekly monitoring of supplies that fell to key department resources. Johnna Moeller, Maintenance Clerk at APC, says that “SupplySentry has been a great addition to the facility. It has taken several items off my plate while still ensuring that we do not run out. It has also helped with the consolidation of supplies and the amount of time and labor it takes to place PO’s for multiple vendors to order everything we need.”
Jamison adds that “SupplySentry’s flexible options easily adapt to the specific environment and also allow for quick adjustment to our changing needs. Generally, a SupplySentry System can be installed and operational on the same day. And RFID requires minimal employee training to ensure system effectiveness.” Dave Neiman, President & CEO of APR, comments, “American Packaging’s use of SupplySentry has grown as our technology has improved. They are very much a company that has focused on efficiencies throughout their organization, and we believe that the benefits of SupplySentry fit well within this philosophy. We are thrilled that they have expanded the number of products we manage, increased the size of the installations, and added other facilities to it.”
APC estimates that they conservatively save 10-15 hours per week by having the system at each facility. There is a reduction in physical inventory and managing supply outages, and they incur secondary cost savings by eliminating expedited shipments. Jamison concludes that “SupplySentry has allowed APC personnel to focus on operations without concern of critical inventory supply issues. With the variability of order changes, this has had a positive impact on our customers. It ensures we do not delay or miss job dates due to internal supplies availability. As a fairly lean company, this has really allowed APC to focus resources on daily production demands versus supplies management.”
Download - American Packaging Case Study, Adobe PDF, 182KB