Glenroy, Inc. and APR’s SupplySentry –
Transforming Inventory Management
Overview
Glenroy, Inc., a growing leader in renewable packaging solutions, recently faced the challenge of efficiently managing inventory for their non-production supplies. When their inventory manager of over 35 years decided to retire, Jon Nagel, Glenroy’s Technical MRO Buyer, was asked to take on the additional responsibility. The previous manager had meticulously managed these supplies, knowing each department’s requirements and usage, and relied on manual stock checks and reordering. However, Glenroy’s growth demanded a more automated solution to reduce the hours spent on inventory checks and minimize the risk of stockouts or overstocks.
The Challenge
As Glenroy works to balance the family-owned feel of a small company with the modern manufacturing standards of a significant player in the industry, the demands on inventory management became more complex. With a sizable facility and growing needs, the company sought a partner that could not only meet their inventory needs but also provide a price-competitive and flexible solution to streamline their stocking process.
The Solution: APR’s SupplySentry Program
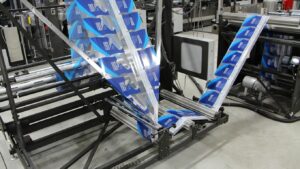
Glenroy chose APR’s SupplySentry program for its price neutrality, inventory automation capabilities, and the company’s commitment to being a partner rather than just a supplier. Jon appreciated that APR offered solutions tailored to Glenroy’s needs, ensuring that supplies would always be available without requiring manual checks and restocking.
APR’s team handled every aspect of the SupplySentry setup, from shipping and installing the system to testing and troubleshooting in the initial weeks. APR’s hands-on approach was essential during the learning period, addressing minor setup issues quickly and effectively.
According to Jon, “SupplySentry has simplified our inventory process. We’re no longer spending hours on stock checks and reorders. APR’s proactive approach and support have given us peace of mind and allowed us to focus more on production and less on inventory."
Implementation and Results
With APR’s SupplySentry program, Glenroy saw a significant transformation in its inventory management process:
- Labor Savings: The automated system saved Glenroy approximately 15+ hours each week by eliminating manual stock checks, ordering, and restocking.
- Enhanced Product Availability: Glenroy now stocks around 20 different types of tapes and six sizes of doctor blades, with lead operators able to pull inventory directly from SupplySentry locations in their production areas, keeping workflows uninterrupted.
- Improved Issue Resolution: When Glenroy identified an issue with a masking tape not adhering as expected, APR quickly responded with alternative products for testing, resolving the problem within a month. This proactive support helped maintain smooth operations and fostered trust in APR’s partnership.
- Cost Savings: APR not only provided equivalent products at competitive pricing but also recommended cost-effective alternatives and cost-saving solutions that allowed Glenroy to consolidate SKUs.
- Ongoing Support and Customization: APR actively monitors Glenroy’s usage patterns and reaches out proactively to suggest adjustments to their min/max levels.
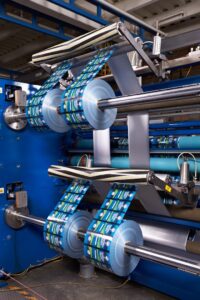
Conclusion
Glenroy’s partnership with APR has transformed its inventory management into an efficient, hands-off process, allowing Jon and his team to focus on core operational goals without worrying about stock shortages or overages. APR’s SupplySentry program proved to be a highly adaptable and responsive solution that aligned perfectly with Glenroy’s growth needs and commitment to operational excellence.